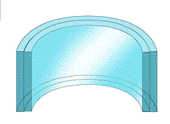
Laminated glass consists of two pieces of glass bonded together by a plastic interlayer. Unlike other forms of
monolithic glass, glass fragments are retained after breakage. This post-breakage condition enables laminates to
provide safety in the case of accidental impact, minimizing cutting and/or piercing injuries. Laminated glass
interlayers include polyvinyl butyral (PVB), ionoplast, polyurethane (PU), and ethylene vinyl acetate (EVA).
Manufacturing
Laminated glass is typically made via an assembly line process that is followed by controlled exposure to heat and
pressure in an autoclave. Curved laminates are assembled and then encased in vacuum bagging prior to
autoclaving. The process for making cast-in-place resin laminates varies based on the resin. For instance, a
laminate may require exposure to UV lights to fully cure. Other resin laminates may require different curing
techniques.
Glass Types
All glass types can be laminated. The basic safety laminate consists of two plies of annealed glass. Some
architectural and transportation applications require the glass to be heat or chemically strengthened, or tempered,
for greater strength, as well as better resistance to thermal and mechanical stresses. Clear, tinted, and low-E
glasses can be laminated. Laminated glass can be part of an insulating glass unit for greater mechanical and
thermal performance.
Interlayer Types
Interlayers fall into two categories, flexible and stiff. Polyvinyl butyral (PVB) is an example of a flexible interlayer.
Within this category, there are standard safety interlayers and those specifically designed for sound attenuation,
security, and solar performance. Ionoplast interlayers are stiff interlayers—100x stiffer than standard PVB and five
times more tear resistant. Besides its strength, ionoplast interlayer is less moisture sensitive, an important feature
with open-edge glazing systems. It is important to confirm the compatibility of all coatings, frits, sealants that will
come in direct contact with the interlayer.
Interlayer features
Most interlayers filter up to 99% ultraviolet below 380 nm. This feature enables laminates to help minimize fading
of fabrics and furniture caused from UV exposure. In addition, interlayers are available in clear or tints. The tints
are often used to minimize glare from excessive sunlight. Interlayers are available in a variety of thicknesses from
0.015 inch to 0.090 inch. For instance, an 0.015-inch interlayer may be used in a transportation side lite
application, but 0.030 inch is required for windshields. Architectural laminates made with annealed glass for safety
glazing typically incorporate a 30-mil PVB or 35-mil ionoplast interlayer. When heat-strengthened or fully
tempered glass is laminated, a 60-mil interlayer is used. Skylight glazing and laminated glass railings will generally
require a 60-mil interlayer. Thicker interlayers may be required for other security applications. The quality
requirements for laminated architectural glass are found in ASTM C1172. This standard sets tolerances on
blemishes that can occur during fabrication, including boils (bubbles), blow-ins, hair/lint, inside dirt, and short
interlayer scuffs (streaks).